This Robot’s Gentle Grip Can Harvest Berries and Other Delicate Fruit
Jun 10, 2022
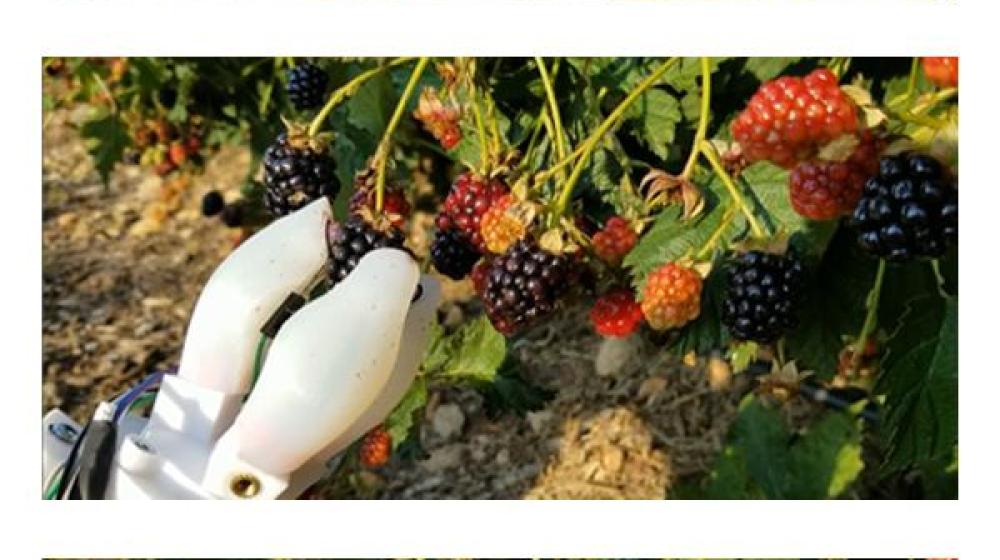
Harvesting a field full of fragile blackberries is no easy task.
Each of those juicy berries sold in the grocery store produce aisle has to be collected by hand because the fruit can be easily bruised or ruined altogether. Here in the South, the harvesting window happens right in the midst of the hot summer months. Plus, all of the berries on a single bush won’t necessarily be ripe for the picking at the same time, so it may take multiple pickings to gather all the fruit.
Biomedical engineering roboticist Yue Chen is working with collaborators at Georgia Tech and the University of Arkansas on an autonomous robotic solution to this backbreaking work. And though it’s a tool that seems far from the traditional purview of biomedical engineering, the system could lead to innovations in minimally invasive surgery one day.
“Harvesting is a very good entry point to validate this kind of soft robotics technology in real-world applications,” said Chen, assistant professor in the Wallace H. Coulter Department of Biomedical Engineering at Georgia Tech and Emory University.
“I’m a medical-device person; I’m trying to develop a device that’s very dexterous, that’s very compliant to save patients’ lives. I deal with a lot of math, engineering, and mechanics problems, and from that perspective, taking berries from a plant is quite similar to removing a tumor from the body,” he said. “You want to identify a target, perform the path planning, reach the target, remove the target very gently, and, most importantly, avoid damaging the surrounding tissue, like a blood vessel or a nerve.”
The researchers’ first advance is a soft robotic gripper that can gently grasp and remove blackberries from the plant — damage-free. They’re presenting the device this week at what’s billed as the largest robotics research gathering in the world, the IEEE International Conference on Robotics and Automation.
The prototype gripper resembles a bulbous three-fingered hand, which is no accident. Working with experienced blackberry researcher Renee Threlfall at the University of Arkansas, the team built a sensor glove and collected data about the force required to harvest berries and pickers’ typical technique.
“First we characterized how much force the hand is generating, how many fingers we use to grasp the berries — we actually don’t use all five fingers, we use three fingers to grasp, and we characterized all of that,” Chen said.
With the force data and the three-fingers insight, Chen and the team set about designing. They used the human hand for inspiration, ultimately using soft silicone and embedded force sensors for the “fingers” and a unique tendon system for movement.
“The human hand has tendons in the fingers that help you bend and move. So, we developed tendon wires, and when we pull the tendon wire, the gripper can bend,” Chen said. “That allows the three fingers to form a close grasp of the object.”
In addition to Threlfall, Chen’s team included Georgia Tech graduate students Anthony Gunderman and Jeremy Collins plus Arkansas food science graduate student Andrea Myers. Together, they published details of their work in April in IEEE Robotics and Automation Letters.
Now Chen is adding more Georgia Tech collaborators to his team — Ye Zhao in mechanical engineering and Ai-Ping Hu in the Georgia Tech Research Institute (GTRI) — to take the next steps with the gripper, including making it mobile and able to move autonomously through fields. They have new seed funding from GTRI, the Georgia Tech Institute for Robotics and Intelligent Machines, and Georgia Tech’s Executive Vice President for Research to continue the work and pursue external funding from agencies like the National Science Foundation and U.S. Department of Agriculture.
The researchers also plan to explore other types of agriculture where their innovations could be useful, including a particularly famous Georgia product.
“One of the very interesting applications is harvesting peaches. Most of our fresh market peaches, they’re still harvested manually. There's no kind of robot to harvest them, because peaches have a very fragile surface,” Chen said.
“We’re working to optimize our system to make sure it’s more generalized. Blackberries are challenging, because they’re very small and the surface is very fragile. But if we’re successful with blackberries, we can extend to peaches, as well.”
This research was supported by the Georgia Tech Institute for Robotics and Intelligent Machines, the Georgia Tech Research Institute, and the University of Arkansas Chancellor’s Innovation and Collaboration Fund. Any opinions, findings, and conclusions or recommendations expressed in this material are those of the authors and do not necessarily reflect the views of any funding agency.