RBI affiliated researchers attend nanocellulose workshop on advancing commercialization
May 20, 2019
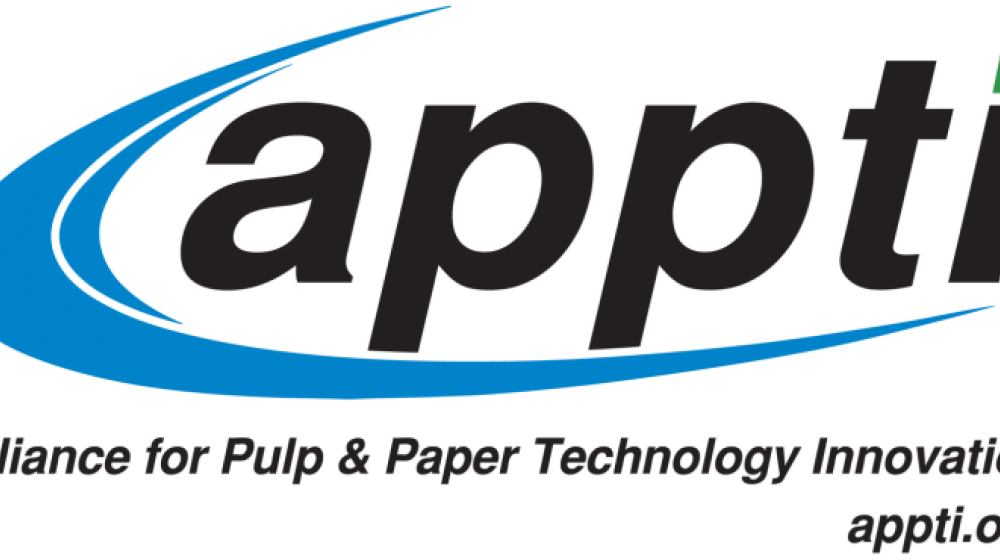
RBI affiliated researchers attend nanocellulose workshop on advancing commercialization
WASHINGTON, DC — The Alliance for Pulp and Paper Technology and Innovation (APPTI), in collaboration with the USDA Forest Service and the National Nanotechnology Coordinating Office (NNCO), held a workshop Advancing Commercialization of Nanocellulose – Critical Challenges,May 7-8 in Washington, DC. Sixty-six people from 44 companies, five government entities and 14 universities participated in the event.
Georgia Tech’s Renewable Bioproducts Institute (RBI) was represented by several researchers and faculty, including RBI’s Interim Executive Director and Associate Professor Meisha Shofner(MSE), Professor Carson Meredith(ChBE), Professor Yulin Deng(ChBE) and Senior Research Engineer Scott Sinquefield.
The two-day session was devoted to determining critical knowledge gaps and research needs which, if overcome, would have the greatest impact on accelerating widespread implementation and commercialization of nanocellulose materials and applications.
"The workshop was an important venue for continuing the conversation about realizing the potential of nanocellulose,” Shofner said. “It brought together diverse stakeholders in the nanocellulose area to address some key challenges in the field and provided opportunities to learn more about the capabilities of these stakeholders, including RBI."
Presentations of two literature reviews focused on those very challenges were delivered on compatibilization and on drying & dewatering by lead authors Greg Schueneman (U.S. Forest Service) and Sinquefield, respectively. These reviews were commissioned well in advance of the workshop and addressed two well-known grand challenges in commercializing of nanocellulose. They are now being prepared for publication.
The context centered on nanocellulose being produced in aqueous suspensions of only a few percent solids and becoming very viscous with increasing solids content. Even a 10% nanocellulose suspension takes the form of a thick paste, not conducive to pumping or spraying. Effective drying and dewatering processes will greatly reduce transportation costs. However there is a high degree of surface reactivity that must be preserved. The second paper by Sinquefield, “A Review of Nanocellulose Drying and Dewatering,” concluded that no conventional commercial drying unit operation alone has been found to be adequate. Nanocellulose fibrils and crystals have a high concentration of surface hydroxyl groups, which form intra-fiber bonds during drying resulting in agglomerates that resist redispersion following drying.
“Various additives have been found that sorb to active surface sites and prevent the fibers from re-combining. These additives tend to be costly and require complex processing, including recovery for reuse,” Sinquefield said. “The cost is justified for high value products, but more research is needed to develop low-cost methods of drying and dewatering nanocellulose such that it can completely redisperse in either water or non-polar mediums.”
The knowledge gaps and research needs were further prioritized at the workshop.
Alexander Friend, deputy chief of the U.S. Forest Service, cited the encouraging increase in nanocellulose production volume to 20,000 tons per year. He noted that the Forest Service’s investment contributions in developing US production capability represented a commitment to nanocellulose “to sustain the health, diversity, and productivity of the nation’s forests and grasslands to meet the needs of present and future generations.”
Small groups identified and prioritized research needs to address remaining knowledge gaps in the areas of compatibilization of nanocellulose with other materials such as plastics, and of drying and dewatering. They then developed potential research approaches that might provide solutions to those needs. Going forward, APPTI and its nanocellulose team, along with its partners, will seek to execute the identified priority projects. Two opportunities for DoE funding were announced recently for which these projects could potentially apply (seeDoE Innovative Manufacturing and DoE BETO Opportunity).
For further information, visit www.appti.org.